Pipe manufacturing is a crucial process within the construction industry as it facilitates the transportation of fluids such as gas, oil, and even water. Steel pipes are a top choice among manufacturers and engineers alike due to their durability, strength, and versatility. One of the types of steel pipe that is commonly used today is the straight seam welded steel pipe. In this article, we will delve into what straight seam welded steel pipes are, their benefits, and how they are manufactured, with a focus on thin wall alloy steel pipes.
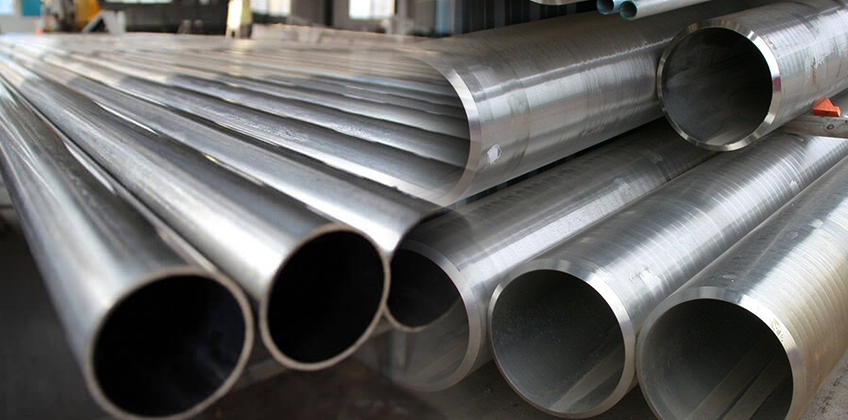
What is a Straight Seam Welded Steel Pipe?
A straight seam welded steel pipe is a type of steel pipe that is formed by welding a longitudinal seam during the manufacturing process. This type of steel pipe has a straight seam that runs the length of the pipe, which is why it is called "straight seam." The seam can be welded using various methods, including electric resistance welding (ERW) and submerged arc welding (SAW).
Benefits of Straight Seam Welded Steel Pipes
Straight seam welded steel pipes provide many advantages over other types of pipes, such as seamless pipes, spiral welded pipes, or longitudinal submerged arc welded (LSAW) pipes. Some of the benefits of using straight seam welded steel pipes include:
1. Cost-Effective: Straight seam welded steel pipes are known for their cost-effectiveness, as they are cheaper to manufacture compared to other types of pipes.
2. Versatile: Straight seam welded steel pipes are suitable for a wide range of applications, including gas, oil, water, and even the transportation of solids.
3. Strong and Durable: Straight seam welded steel pipes are known for their strength and durability, which is why they are commonly used in the construction industry, particularly in the development of infrastructure projects such as bridges or buildings.
Manufacturing Thin Wall Alloy Steel Pipes
Thin wall alloy steel pipes have a diameter that is considerably smaller than most other steel pipes. The manufacturing process of thin wall alloy steel pipes is similar to that of other straight seam welded steel pipes. However, due to the smaller diameter of the pipes, there are some differences, particularly in terms of the thickness of the pipes.
The manufacturing process of thin wall alloy steel pipes begins with the production of raw materials such as alloy steels, which are then formed into a tube shape. The tube is then fed into a machine, where the edges are welded together to form a continuous seam. The welded tube is then passed through a variety of rollers, which compress the pipe and reduce its thickness. This process continues until the desired thickness is achieved.
Thin wall alloy steel pipes are versatile and are commonly used in industries that require high-strength pipes that can withstand high temperatures and pressure. Due to their thinner walls, these pipes offer improved flow rates, making them ideal for applications that require a high flow of fluids or gases.
Conclusion
In conclusion, straight seam welded steel pipes are an essential component in the construction industry. Versatile, cost-effective, and durable, they have a wide range of applications, including the transportation of gas, water, and even solids. With the advent of thin wall alloy steel pipes, engineers and manufacturers have more choices when selecting pipes that meet their requirements. The unique properties of thin wall alloy steel pipes make them ideal for use in industries that require high-strength pipes that are reliable and can withstand high temperatures and pressure. Materials such as 20#, Q345B, GR. B, X42, X56, P11, P22, ST37, ST45.8, ST52, S235JR, and S355JR are commonly used in the production of thin wall alloy steel pipes. The inclusion of keywords such as thin wall alloy steel pipe in this article aims to increase the visibility of this topic and promote further discussion on this crucial component in the construction industry.