Selecting and sizing pneumatic and hydraulic components requires careful consideration and planning. The right components will ensure that the system operates at peak efficiency, while the wrong components can lead to premature system failure, safety hazards, and increased maintenance costs.
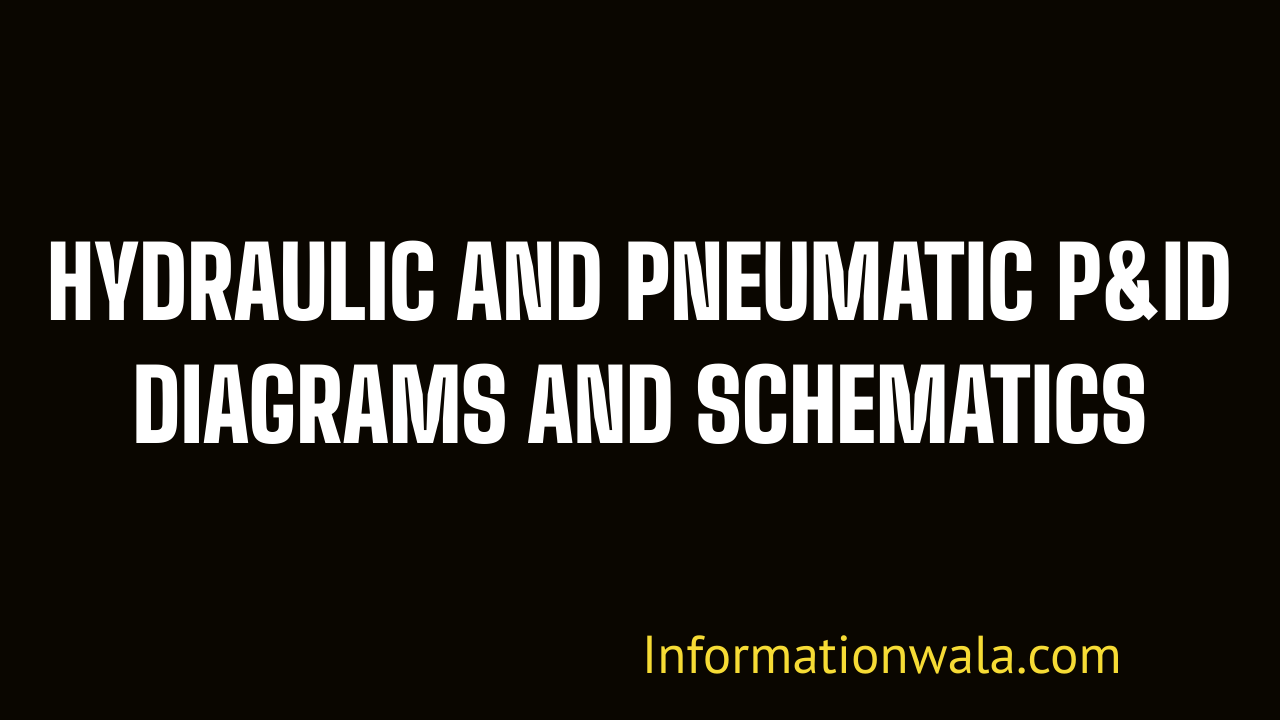
Here are 12 tips for selecting and sizing pneumatic and hydraulic components:
1. Define the operating parameters: The first step is to define the operating parameters of the system. This includes the required force, speed, and stroke length that the system must deliver.
2. Determine the necessary flow rate: The required flow rate of the system is critical in determining the size of the components. It is important to ensure that the flow rate is not too high or too low for the components.
3. Select the right cylinder type: Different cylinder types have different advantages. It is important to choose the right cylinder type based on the specific application requirements.
4. Consider the load type: Different loads require different cylinder types. It is important to choose the right cylinder type for the load type.
5. Choose the right actuator: The actuator type is critical in determining the operating parameters of the system. It is important to choose the right actuator type based on the specific application requirements.
6. Select the proper valve type: The valve type is critical in determining the control and flow of the system. It is important to choose the proper valve type based on the specific application requirements.
7. Determine the necessary pressure: The required pressure of the system is critical in determining the size of the components. It is important to ensure that the pressure is within the operating limits of the components.
8. Use the right fluid: Different fluids have different properties. It is important to choose the right fluid based on the specific application requirements.
9. Consider the temperature range: Different components have different temperature ranges. It is important to choose components that can operate within the necessary temperature range.
10. Calculate the necessary power: The necessary power of the system is critical in determining the size of the components. It is important to ensure that the components can handle the necessary power.
11. Consider the environment: The environment in which the system will operate is critical in determining the components. It is important to choose components that can withstand the necessary environment.
12. Consult with experts: Consulting with experts in pneumatic and hydraulic systems can provide valuable insight and guidance in selecting and sizing components.
Selecting and sizing pneumatic and hydraulic components may seem overwhelming, but with careful consideration and planning, it can be done effectively. Remember to define the operating parameters, determine the necessary flow rate, choose the right cylinder type and actuator, select the proper valve type, calculate the necessary power, and consider the environment. By following these 12 tips, you can ensure that your system operates at peak efficiency and avoids premature failure.